Boards
http://m.mk.co.kr/news/company/2014/1166501
http://star.mk.co.kr/v2/view.php?sc=40900001&cm=%EC%A2%85%ED%95%A9&year=2014&no=1168623&relatedcode=
두 기사를 보시면
사고차의 뒷바퀴가 자세히 보이는데
아무리 봐도 이상합니다.
외부충격에 의한 것은 분명 아닌 것 같구요
정비불량이라고 해 봐야 휠 너트를 조이지 않았을 가능성 뿐이라고 보는데
사진상으로 보면 휠너트들이 다 부러진 것으로 보이는데?
구글신으로 검색중 스타랙스 차종에서 유사한 사고사례가 있는 것을 발견했습니다.
http://www.kidi.or.kr/pdf/%EC%A0%84%EB%AC%B8%EC%9E%90%EB%A3%8C/KIDI_20070828_10946.pdf
아직 정확하게 밣혀진 것은 없지만
만약 제조 결함이라 하더라도
우리나라 실정에서 제작사에 제대로 책임을 물을 수 있을까요?
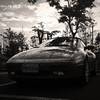
정비를 어떻게 잘못 해야 저렇게 될 수 있는지 궁금하더라구요.
국과수에서 결과 나와도 현대에서 믿을 수 없다고 버틴 사례도 있는데, 이번껀 어떻게 처리될지...
전복사고라면 네바퀴 모두 온전하기 힘들지 않나요? 50키로 주행시에도 앞이 보이지 않을정도의 비가 왔다는데.. 아무튼 몇장의 사고후 사진으로는 판단하기 힘들거 같아요.
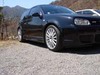
렌터카 업체도 큰 회사로 알고있는데 첫 운행이었다면 정비보다는 생산과정에서의 문제가 아니었을까 싶습니다.
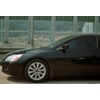
사진상으로는 액슬 너트로의 수분침투를 막기위한 덮개가 그대로 붙어있는 것으로 보아, 허브베어링은 붙어있고, 주위의 디스크 결합 플랜지 부분이 떠러져나간것 같았습니다. 당연히 디스크와 휠은 붙은 채로 떨어져나간듯 보였구요. 디스크가 캘리퍼에 물린채로 이탈하였으므로 캘리퍼 브라켓이 휘어진 상태가 어렴풋이 확인가능하였습니다. 즉, 허브베어링 유닛이 깨져 떨어져나간듯 보이는데요, 이게 왠만하면 깨지지 않는 안전률 마진이 꽤나 높은 부품이라는겁니다.. 주조공정에서 공기방울, 크랙 조금 들어간다고 저리되진 않을 부품인데요.. 또한 사고 시 연석등에 휠이 횡방향으로 충돌하면, 허브베어링 유닛보다는 너클 채로 떨어져나가는 경우가 다반사입니다. 여러 방향으로 생각해보았지만 도통 원인을 알 수 없겠드라구요..
군생활때 카운티와 문제의 그랜드스타렉스를 몰고다녔었는데,카운티는 조립불량 차들이 꾀 많습니다.06년식은 에어컨물이 운전석으로 떨어졌었고...vip 12인승 버젼이 뒷좌석쪽에 물이새질않나...조수석에 물새던 차도 2대있었네요. 13년식은 4000km때 심지어 깜빡이등 고정 나사가 풀리는 바람에 빠져버렷던 차도 있습니다. 마찬가지 13년식 VIP 12인승 카운티도 제 후임이 운행나가다가 헨들이 털려서 세워보니 휠 너트가 2개 풀렸답니다 ㅎㄷㄷ;; 휠을 한번도 푼적없고 운행도 잘않하던 쌔차였는데 풀려버렷다더군요.(당시 휠커버가 씌어져있었습니다)
그랜드스타렉스는 제가 실무에 복무하던 21개월동안(2개월은 훈련;;) 터보차져 파이프가 3대나 빠져버렷고 다른 소대 6밴차량도 파이프가 2대정도 잘가다가 빠져버렸다더군요. 그리고 12년도이후였나?? 여튼 이후 출고된 년식좋은 차량은 원가절감 때문인지 문을 닫으면 텅~~~~~ 하는 빈깡통 소리가 낫었습니다. 09-10년식은 않그런데말이죠 ㅎㅎ
전역이후론 현대차 얼씬도 않합니다;;
솔직히 저사진으로 판단할수 있는 건 없어보입니다..
국과수에서 분석한다니 기다려보시는게.ㅈ.
휠이 빠졌으면, 차체바닥 부분이 일부 쓸려나갔을 겁니다. 차량을 조금이라도 살펴보면 과속으로 스핀하여 굴렀는지, 뒷바퀴가 먼저 빠졌는지 알 수 있을겁니다.
다만 차량 사진을 보면, 앞바퀴 조차도 링크가 거의 다 떨어져나가 전복 시 상당한 충격이 있었을 것으로 예상됍니다. 마찬가지로 뒷바퀴가 떨어져나간 이유에 대해 개인적으로는 스타렉스 리어액슬 구조에 힘을 받는 부위 중에 허브 고정부위가 가장 취약해서 그럴 수도 있다고 생각합니다. (절단면이 피로파괴면 당연 정비 불량)
소속사도 뒷바퀴가 빠졌다고 발표했다가 서둘러 철회한걸 보면 섣불리 차체결함으로 보긴 어렵지 않나 싶습니다.
개인적으로 BMW 520D를 시속 90으로 경부고속도로 양재 부근에서 물웅덩이 밟고 180도 스핀하여 무시무시한 경험을 한 적이있는데 스타렉스 운전하시는 분이 평소 카니발(전륜)에 익숙하여 후륜의 빗길 주행 리스크를 간과한 부분도 없지 않아 있지 않을까 싶습니다.
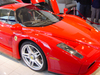
휠이 사고 후에 빠지든...전에 빠지든..
에어백은 안터진걸로 보이네요..;;;;멋지다..;;;뭐 또 조건이 안맞았남..;;;
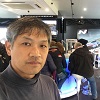
사고전에 바퀴가 빠졌는지.. 전복되고 나서 바퀴가 빠졌는지는 모르겠습니다만 주행중에 바퀴가 빠지는 일은 '절대 있을 수 없는 일'은 아닙니다. 아래 동영상 보시죠.
이런 케이스에 대한 전문가의 의견은 이렇습니다.
http://www.denenapoints.com/library/more-on-wheel-hub-failure-caused-by-metal-fatigue.cfm
또다른 구글링의 결과는 아래와 같네요.
Crash Forensics provides wheel and hub failure analysis services for passenger vehicles and heavy trucks. Failure analysis services can be conducted "on site" from our mobile lab or "in house" in our automotive lab. Below is a discussion of wheel and hub failures. Link to our automotive expert.

Crashes caused by wheels coming off of vehicles are commonly referred to as wheel runoff crashes. Two primary failures cause wheel runoff crashes. One is a failure of the wheel mounting system, such as the wheel studs, lug nuts, etc. The other cause is a failure of the hub and wheel bearing assembly. Most commonly, these failures are related to improper or deferred maintenance, but some are also linked to manufacturer's defects.
Wheel System Failures
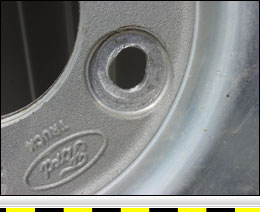
Wheel system failures are primarily caused by the improper installation of a wheel that causes it to be loose or become loose. Commonly, a loose wheel causes the wheels studs to break and the wheel and tire to separate from the vehicle. Many root causes lead to loose wheels, but most of them are associated with over-torquing or under-torquing the lug nuts.
A bolted joint, such as a wheel mounting system, works by tightly clamping two surfaces together. The friction of the two mated surfaces and the force created from clamping them together with bolts (Clamp Load) allows the surfaces to resist movement. The amount of friction and Clamp Load determines the level of resistance the joint has to movement.
Clamp Load is created by tightening the bolts against the mated surfaces and is normally measured in foot pounds of torque with a torque wrench. If the bolt torque specified for a joint is applied, then the resultant Clamp Load should also be within specification. However, variations in the system such as rust or lubrication on the threads can affect the Clamp Load vs. torque relationship. Items in place between the mated surfaces can reduce the joint's friction and also alter the relationship between bolt torque and Clamp Load. This is called a Soft Joint.
Two concepts are important to understanding how a bolt works. They are Elastic Deformation and Yield Point. Elastic Deformation is metal's or, in this case, a bolt's ability to stretch and spring back to its original shape. Yield Point is where the bolt has been stretched past its elastic limit and can no longer spring back to its original shape. This stretching of a bolt and its pulling back creates Clamp Load. If, however, a bolt is over-torqued, and stretches past its Yield Point it can no longer maintain the Clamp Load.
Over-torquing is likely the most common wheel system failure due to the widespread use of impact wrenches to install wheels. Using an impact wrench to install wheels commonly causes the wheels to have 3 to 5 times the specified lug nut torque. The use of lubricants and anti-sizing compounds on the threads of the wheels studs or lug nuts can cause an even higher degree of over-torquing.
The specific torque required to install a wheel varies from vehicle to vehicle. Generally, the proper torque for the lug nuts on passenger vehicles will be around 100 foot-pounds and the proper torque for big trucks will be around 400 foot-pounds. Impact wrenches commonly used to install wheels on passenger vehicles are capable of producing 300 to 500 foot-pounds of torque. Impact wrenches used to install wheels on big trucks can produce 1200 to 2000 foot-pounds or torque.
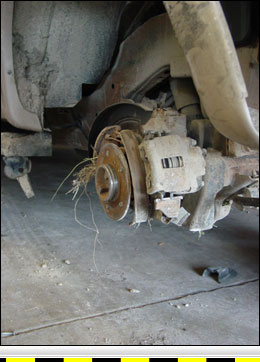
Under-torquing is just simply not tightening the wheel lug nuts enough, causing the wheel to be loose. Under-torquing can be caused by corroded and damaged wheel system components. It can also be caused by using a cheap or worn-out impact wrench or by having a low air-pressure supply to an impact wrench.
Another common cause of wheel system failures is too much wheel paint thickness. As specified by the Recommended Practice PR222B from The Maintenance Council (TMC) of The American Trucking Association "Total thickness of the dried paint coating on each side of the wheel mounting face must not exceed 3 mils (.003 inch)." If the wheel's paint is too thick, then a soft joint is created and the system can fail.
Paint thickness defects are not only caused by original production painting but also more commonly caused by the recondition or "remanufacturing" of wheels. Wheel reconditioning generally involves "sandblasting" used truck wheels and repainting them to make them look new. The reconditioning of wheels is typically being done by tire dealers and tire retreaders who do little to control paint thickness.
Hub Failures
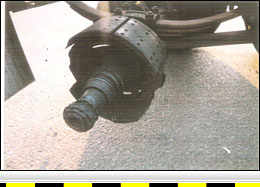
There are four primary causes of hub failures. They are lack of lubrication, overloading the vehicle, installing the axle nut too tight, or installing the axle nut too loose. Usually, hub failures are progressive and will produce some evidence of the impending failure. Evidence of a failing hub can include leaking hub seals, tire tread wear anomalies, sounds, smells, smoke, and steering wheel feedback.
The bearing preload is adjusted by tightening the axle nut down against two cone-shaped bearings. As the nut is tightened, the hub assembly becomes tight and the play is removed from the system. Once the bearing preload is adjusted, a lock is installed to prevent the axle nut from moving. Although, there are many types of locks for axle nuts, some common ones are a cotter pin placed through a castled hex nut or a keyed washer placed over a flat hex nut followed by a second nut to hold the washer in place.
The proper method for adjusting and preloading bearings has 5 to 8 steps, but is rarely followed. Here is an example of one methedology published by the bearing manufacturer Timken:
- Torque the adjusting nut to 200 lb-ft to seat the bearing components. Always rotate or oscillate the wheel while torquing the adjusting nut to ensure that the rollers are fully seated against the cone large rib.
- Back off the adjusting nut one full turn or until it's loose.
- This is where you actually establish end play. Torque the adjusting nut to 50 lb-ft while rotating the wheel hub assembly.
- Back off the inner (adjusting) nut the appropriate amount as indicated by the chart at right; e.g., 1/6 of a turn for a 12-threads-per-inch front steer axle. See chart at right for the exact back-off amount.
- On a single-nut system, install a cotter pin. On a double-nut system install a jam nut and torque it to the proper specification, which varies depending on the size of the nut.
Once these steps are preformed, also recommended is that the hub's end-play be measured with a dial indicator to verify proper preload.
A hub that is adjusted too loose will allow the hub and wheel assembly to oscillate laterally. This will cause bearing wear and will cause a further increase in hub looseness. The loose hub allows excessive movement of the bearing rollers resulting in roller cage wear and uneven race wear or "scalloping". If not repaired, the bearing play will increase progressively to the point where the hub fails.
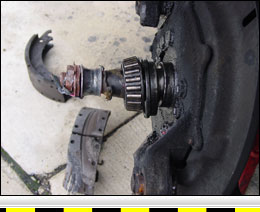
A hub that is adjusted too tight will not have a lubricant barrier between the bearing rollers and bearing races. Without a lubricant barrier, the bearing will overheat and fatigue. This condition will lead to full bearing lock up and hub separation if not corrected. This condition will be evidenced by heat discoloration and fatigue spalling on the bearings.
Overloading a hub creates similar conditions as over-tightening the hub. The excessive weight forces the lubricant from between the bearing rollers and bearing races on the loaded side of the bearing causing localized heat and fatigue.
Lack of lubrication also causes metal to metal contact between the bearings and races. This results in excessive heat, bearing and race scoring, and microspalling fatigue. This condition, if not corrected, will lead to bearing lock up and hub separation.
The mechanism of failed hub separation can vary by the design of the hub. Some hubs have a small outer bearing and axle nut. When the outer bearing fails, the hub can just slip past the axle nut and remaining parts of the outer bearing. In hubs with large outer bearings, separation of the hub occurs when the oscillating hub causes the axle nut to be pulled off the axle like a bottle cap. In other cases, the axle nut is pulled off the axle, ripping the threads out of the axle nut and leaving the threads on the hardened axle relatively undamaged.
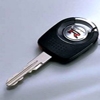
벨로스터 터보 타면서 바퀴 빠져본 경험이 있습니다. 허브가 완전히 부러졌더라구요. 어떤 충격이나 사고가 있지 않은 상태에서 바퀴만 빠졌습니다.
정비소에서 위치교환한 적도 없는 새차였는데 고속도로에서 고속주행 하다가 직진성이 이상하고 핸들을 조타하면 좌우로 반동이 계속 느껴져서 이상하다 생각해서 가까운 ic로 차를 빼서 정비소로 가던 도중에 시내주행 50km/h 상태에서 교량을 지나면서 뒷축이 빠져버리더라구요. 그때 차가 반정도 스핀할려고 했는데 주변에 차도 없고 해서 브레이크 안밟고 핸들 조타만으로 차량 중심을 어떻게든 살리고 엔진브레이크 써서 최대한 감속후 차를 세울 수 있었습니다.
현대에서 나온 결론은 운전자에 의한 하체 충격에 의해서 바퀴가 부러졌다고 결론을 내리더라구요.
일단 바퀴가 부러지면 메이커에서는 증거를 잡기 어렵기 때문에 말하기 나름인 거 같습니다.
이번 스타랙스 사고도 차체결함으로 인한 바퀴가 빠졌을 가능성도 있습니다만 정비한적도 없는 차인 경우도 자기잘못이라고 인정을 안하는데 어느정도 주행한 렌트카의 경우 빠져나올 구멍은 더 쉽겠죠.
저도 고속도로에서 괜찮겠지 하는 마인드로 그대로 주행했다면 정말 골로 갈뻔했습니다.
저도 예의주시해 보고 있어요.
참 안타까운 일이예요
마지막 부분... 저도 그게 궁금해요.